What Are the Main Advantages of a Condition Monitoring System?
Maintenance does not always mean repairing your assets and equipment but lots of organizations think in that way. As we know repairing assets can be costly, so organizations keep using assets until asset breakdown. As a result, they have to pay more maintenance expenses. But with a condition monitoring system, you can always keep your assets maintained.
In this blog, we will know what a condition monitoring system is and what are the advantages this system provides! So, let us begin.
What Is a Condition Monitoring System?
A condition monitoring system helps the organization in asset condition monitoring in an automated way. It minimizes the chances of sudden failure.
For avoiding unexpected breakdowns, a maintenance approach is used to predict the health and safety of machines using sensor data collected by the machine which measures vibrations as well as other parameters in real-time.
Additionally, it sends an alert when an asset problem or performance issue is identified.
The traditional method of monitoring the condition of assets was focused on vibration analysis. Condition monitoring is a method of proactive maintenance and most importantly it is similar to preventive maintenance.
It permits the scheduling of maintenance as well as preventive actions to be taken to stop any further breakdowns and unexpected downtime. Condition monitoring has a huge market size!
According to Markets and Markets, “The global machine condition monitoring market size is anticipated to grow from USD 2.8 billion in 2022 to USD 4.0 billion by 2027, at a CAGR of 7.8% from 2022 to 2027.”
Recommend To Read: What Are the Challenges Faced While Implementing Condition-Based Maintenance?
What Advantages Does a Condition Monitoring System Provide?
Below we have mentioned a few crucial advantages of the condition monitoring system:
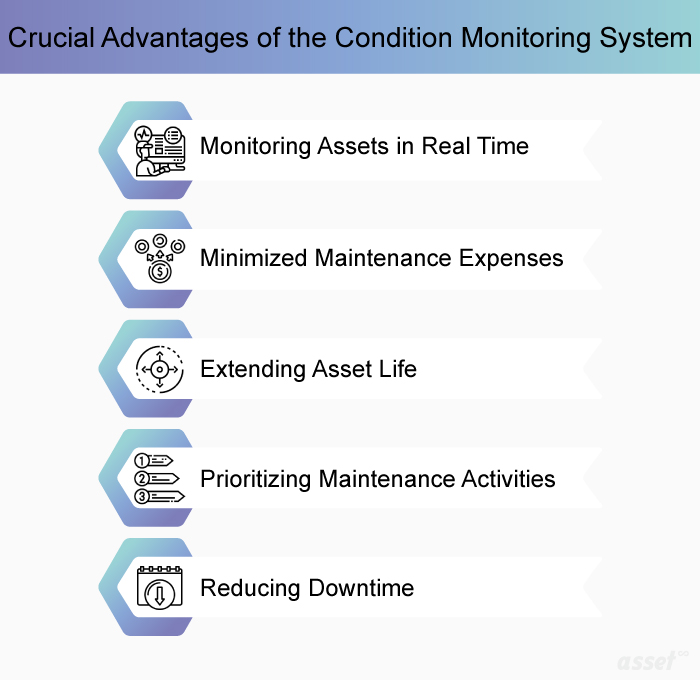
1. Monitoring Assets in Real Time
You can monitor assets in real-time to see their health. Asset maintenance is only delivered when the indicators do not match expectations. These indicators include temperature, vibration, and key performance indicators (KPIs).
Condition monitoring gives you access to an ever-changing pool of data about your machinery. This data can be invaluable in analyzing key performance indicators & can be helpful in enhancing your production work.
This information can help you make informed decisions about equipment performance, purchases, and contracts renewal or not with suppliers.
2. Minimized Maintenance Expenses
As we know, unexpected asset failure is more expensive than regular maintenance as an asset needs to be brought back into running condition as soon as possible.
When you monitor assets in real time you can save a lot of expenses as you can check asset performance and in asset condition monitoring you get lots of data and analytics that help you in better asset monitoring and it is helpful in saving maintenance expenses and you are always aware of asset condition.
3. Extending Asset Life
The prevention of unexpected shutdowns helps protect the equipment's integrity physically by preventing any subsequent harm to the components. The lower the cost of replacing spares, and the higher the longevity of equipment.
If original parts of the asset are not removed, and the assets are maintained, their lifespan grows. Additionally, the extended duration of the equipment results in a lower operational cost.
4. Prioritizing Maintenance Activities
With regular and reliable updates regarding your equipment and assets, you can have a list of maintenance tasks with their priority. This helps you connect with maintenance firms and organize your projects around planned projects that will save time and money.
If the maintenance team does not recognize the priority of the assets, they will work according to the FCFS (First Come First Serve) basis.
This means that the productive work does not get done because important assets are waiting for maintenance which causes time wastage and production delays to occur.
That is the reason prioritizing the maintenance of assets is crucial. You can achieve this with condition monitoring software which is the part of maintenance management software.
5. Reducing Downtime
When assets are given maintenance on time then obviously their performance and uptime improve. Therefore, in order to reduce sudden equipment failure and downtime, it is important to perform maintenance on time.
When you have assets in abundance then it is better to invest in an automated maintenance system such as an asset condition monitoring system.
Conclusion
A condition monitoring system is easy to use but it always needs someone to take care of assets. However, when work is done manually then it becomes more hectic and maintenance work becomes complicated and overdue.
This software notifies the person responsible & provides early warning when an asset is not performing. It enables the organization to provide maintenance before asset failure and work on that issue.
Condition based monitoring says that support ought to possibly be performed when certain limits are reached, or markers give indications of decreasing performance.
The data that this software collects is not just useful for the maintenance team, but it is also helpful for operation staff and fleet managers.
Also Read: Is CMMS the Right Option for Asset Maintenance & Work Orders Management?
Frequently Asked Questions (FAQs)
Q.1 - What Is the Difference Between Preventive Maintenance and Predictive Maintenance?
Preventive maintenance is scheduled maintenance based on asset utilization or time. Whereas in predictive maintenance strategy, an asset is monitored, and performance is noted when that performance starts decreasing and KPIs are not up to the mark then maintenance is performed. Overall, the maintenance expenses are less in predictive maintenance compared to preventive maintenance.
Q.2 - How Is Asset Condition Monitoring Done?
For asset condition monitoring several techniques are used such as analysis of vibrations, sensors are used, engine oil analysis, and temperature of the machine is monitored. These are a few of the techniques used in asset condition monitoring.
Q.3 - What Are the Techniques Used in Asset Condition Monitoring?
With an asset condition monitoring system several asset tracking technologies can be used such as Barcode, QR (Quick Response) Code, RFID (Radio frequency Identification), GPS (Global Position System), BLE (Bluetooth low energy), NFC (Near field communication), IoT (Internet of Things), etc. However, IoT can give the best result because several devices are connected to monitor asset performance.
Note: This article was originally published at Asset
Infinity. You can see the original post here at Condition
Monitoring System
Comments
Post a Comment